We’ve long feared that robots will steal our jobs, and as automation improves, the anxiety grows. This worry is fed by studies from respected scientists, think tanks, and economists that support this view, complete with dark forecasts on human obsolescence.
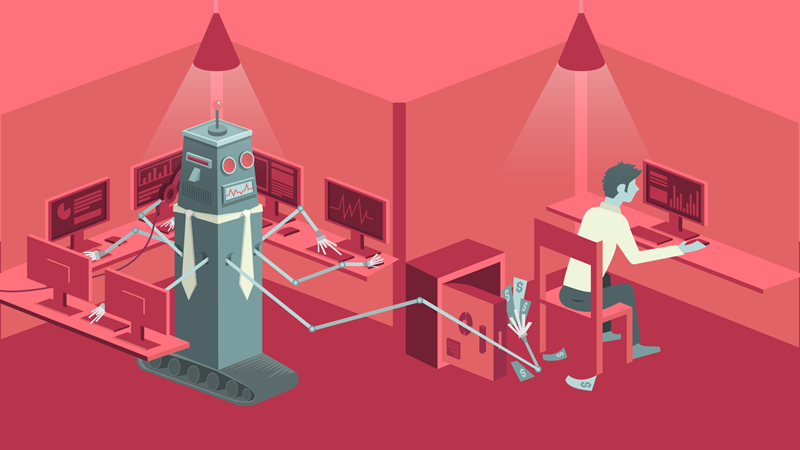
But a recent study of German data by Opportunity & Inclusive Growth Institute senior scholar Sebastian Findeisen and colleagues indicates that the picture isn’t quite so bleak.
“Our analysis finds no evidence that robots are job killers,” they write in “Adjusting to Robots: Worker-Level Evidence,” a working paper from the Federal Reserve Bank of Minneapolis’ Institute. Indeed, increased use of robots has led to higher job stability and greater labor productivity in Germany.
But there are definite downsides: lower wage growth and reduced share of national income to workers, with earnings benefits for those who own capital and firms. “These findings suggest that robots have created aggregate rents but also caused notable distributional shifts in the economy,” the economists conclude.
In a nutshell, workers aren’t made jobless by robots, but those with low- and medium-level skills see less wage improvement over time. Owners and highly skilled workers enjoy higher earnings. Income inequality rises. And the robots grind on.
Three key contributions
The study is noteworthy in several respects. First, it provides a dose of optimism against gloomy predictions of massive job disruption as automatons move in. A 2018 report from the World Economic Forum, for instance, suggests that without retraining only 2 percent of U.S. workers could obtain an equally good job when displaced by robots. And a 2017 study by economists Daron Acemoglu and Pascual Restrepo estimates that for each robot added between 1993 and 2014, U.S. employers eliminated from 3 to 6.2 jobs.
Second, it depicts a possible future for a roboticized United States because Germany already “employs” robots at higher levels—7.6 robots per thousand workers, compared with 2.7 elsewhere in Europe and 1.6 in the United States. (Germany nonetheless retains a large manufacturing employment share, with about a quarter of all German jobs in manufacturing, compared with less than 9 percent in the United States.)
Third, the study’s most novel contribution is its focus on worker-employer employment histories. Like Adam Smith describing a pin factory’s division of labor, these economists track the paths of millions of individual workers to understand a very different division of labor—tasks performed by flesh and blood and those done by circuits and steel.
Tracking robots and workers
The economists use two research approaches to reveal different “margins of adjustment” to the increased use of robots. First, they compare job markets in county-level German regions with differing levels of robot exposure, providing broad insight into the impact of robots on total German employment and worker flows among industries and labor markets as robots move in, or don’t. Second, as mentioned, they look at worker-level adjustment by following employees over time, tracing employment changes after robots are introduced.
These separate approaches highlight two distinct types of worker adjustment to robot use: reallocation (switching to a different company) and new occupation (sticking with the same employer but in a different role).
The regional analysis compares 402 local labor markets, with detailed information on level and type of employment, including industry structure and worker characteristics such as age and gender. The employee-level approach uses German labor market data to track employment histories of roughly 1 million workers from 1994 to 2014. For robots, they use data from the International Federation of Robotics, differentiating among 53 manufacturing industries and 19 others. Some, like auto manufacturers, are highly robot-intensive; others, such as watch and clock makers, use fewer robots now than 20 years ago.
To pinpoint the independent impact of robots, the economists control for other job market influences, including international trade, information and communication technologies, and trajectories of specific industries that were declining or emerging regardless of robots.
Bottom lines
With this body of data and careful methodology, the economists arrive at several key findings. First, robots did reduce labor demand in manufacturing, but those jobs were fully offset by nonmanufacturing jobs, mostly in business services. “In other words, robots have strongly changed the composition but not the aggregate level of employment in Germany,” they write.
By following individual workers, the economists find that they’ve tended to stay with the same companies but in different job roles. “Firms react to automation by changing the set of tasks for their incumbent employees.” And while German manufacturers do replace human labor with robots, this is “solely driven by fewer new jobs for young labor market entrants.” Older workers leave manufacturing jobs as they shift to new responsibilities or retire altogether, but they’re not replaced by younger workers.
Not surprisingly, the economists also find that robots significantly increase labor productivity (output per worker).
Unfortunately, job stability and higher productivity come at the cost of lower wage growth. So workers don’t stop working, but their earnings grow more slowly than before robots joined them on the job, and regions with high robot exposure suffer declining labor shares (pay as a fraction of output). Job losses were higher at firms where industry-level labor union agreements prevented wage adjustment.
Moreover, the bigger economic pie created by increased robot use is not divided equally. While some is shared through increased job stability, a disproportionate portion goes to plant owners and to higher-skilled employees, including managers, legal specialists, technical workers, and scientists. Automation complements their tasks, rather than substituting for them. Significant earnings losses are incurred, particularly by machine operators.
The economists differentiate three skill levels for the German labor market and conclude that it’s actually medium-skilled workers, those with vocational training degrees, who suffer most from robot exposure, though those with less education are also negatively affected.
Robots, then, portend a mixed future. A job, yes; but unless you’ve got the right skills, don’t expect big raises.