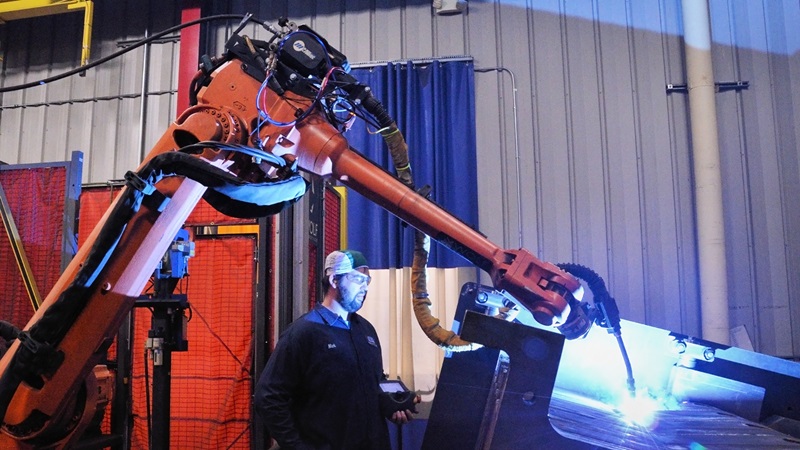
Last year, a new welder joined OEM Fabricators, a western Wisconsin manufacturer of components for oil drilling, transportation and other types of equipment. The newcomer is a real rate-buster, capable of welding steel up to four times faster than its co-workers. What’s more, this welder doesn’t take coffee breaks or vacations, and never gets sick—unless something goes awry with its software or the joints in its mechanical arm need an oil change.
OEM’s super worker is a robot, a 15-foot tall amalgam of articulated steel, cables and circuitry housed in the company’s main facility in Woodville. Scarce skilled labor in the Chippewa Valley provided much of the impetus for the $330,000 purchase, said OEM President S. Mark Tyler. The firm, which employs 270 people in Woodville and two other locations, is close to maxing out its production capacity, partly because of workforce challenges.
“Labor, which we never considered constrained in the past, is constrained today,” he said. “It’s certainly becoming more difficult to bring people onboard. “We used to be able to make a call, and people would come right in. Now, it might take weeks or months to fill a position.”
Installing a robotic welding cell has reduced labor costs and boosted productivity, allowing the company to pursue new lines of business. Recently, the firm landed a contract with a major manufacturer of mass transit vehicles to make a key component of light rail trains. “We are increasing investment in automation and are leveraging that more than we’ve done in the past,” Tyler said.
Workforce challenges and competitive pressures to lower costs and improve quality are inducing many manufacturers in the Ninth District to invest in robots and other forms of automation such as material handling systems and 3D printing. In a survey last fall of district manufacturers by the Federal Reserve Bank of Minneapolis and the Minnesota Department of Employment and Economic Development, 60 percent of respondents said they had increased their use of automation.
Labor advocates and media reports have raised fears that increased automation will put people out of work. Indeed, research by some economists indicates that smart machines may displace some low-skilled workers, at least in the short term.
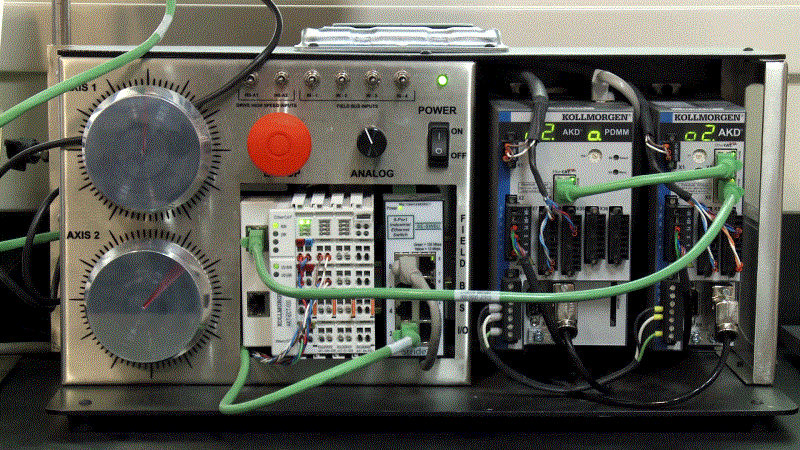
But the automation of manufacturing doesn’t necessarily mean permanent job losses for humans. It’s likely that increased automation will create more, better-paying jobs requiring higher education and advanced skills. The experiences of district manufacturers interviewed for this story bear out this notion; for the most part, higher production and profits achieved through automation have led firms to hire additional workers.
However, the workers in greatest demand on the modern shop floor are those with expertise in robotic programming, system integration and other disciplines needed to play well with machines that sometimes seem to have minds of their own.
Laboring to hire
In many ways, the manufacturing sector is healthier today than at any point over the past decade. The Institute for Supply Management’s February survey of U.S. manufacturing indicated continued expansion in new orders, production and employment. The outlook was similarly sanguine in the district: The Minneapolis Fed manufacturing survey found that firms were upbeat about continued growth this year.
But scarce labor has become an anchor on the growth aspirations of many manufacturers, across the country and in the region. As unemployment rates drift lower—in January, unemployment in Minnesota and Wisconsin fell to the lowest level in 17 years, according to government labor statistics—manufacturers have struggled to recruit and retain employees.
Demographic trends are partly responsible for the thinning of worker ranks—as baby boomers retire, too few younger workers are entering the workforce to replace them. Also, workforce participation rates have fallen, particularly for young men. And manufacturing is still perceived as an undesirable career by many high school students and their parents.
In an effort to attract workers, manufacturers have raised wages—figures from the Bureau of Labor Statistics show that real wages are finally ticking up after years of post-recessionary stagnation—and sweetened benefit packages.
One solution to scarce and increasingly expensive labor is to hand off some operations to machines. Reliable data on adoption of automation by manufacturers is sparse, but the International Federation for Robotics (IFR), an automation trade group, tracks installations of industrial robots—automatically controlled arms and other devices used in applications such as welding, painting, palletizing and product inspection.
A 2017 report by the Brookings Institution that draws upon IFR data found that the number of working robots in the country surged from 2010 to 2015, including in district states (Chart 1). More recent IFR data show that nationwide installations of industrial robots increased 14 percent in 2016, to over 31,000 units. (Also see this interactive U.S. map showing 2015 concentrations of robots in all states.)
In the Minneapolis Fed manufacturing survey, nearly a third of district operators said they had increased automation at their firms over the past year in order to mitigate labor shortages, and a similar share said they did so in order to reduce labor costs.
Manufacturing labor productivity—economic output per hour worked—has lagged since the recession (Chart 2). One explanation for this is slow wage growth during the recovery that reduced the incentive of manufacturers to invest in automation and other forms of labor-saving technology. Now that wages are rising in response to tightening labor supplies, higher costs may be leading manufacturers to reduce their reliance on labor by increasing their use of automation.
“You just have to automate”
Workforce pressures faced by manufacturers have juiced automation sales at Productivity Inc., a suburban Minneapolis provider of precision machining, material handling and other types of equipment to manufacturers in several Midwestern states. Automation products such as robotic arms, vision systems and devices that load and unload milling machines account for a relatively small share of overall firm sales, said President Greg Buck. But that share has “increased every year, and it’s going to continue to increase because there’s just not enough workers in the industry.”
Customers who come into Productivity’s showroom to see automation in action regularly tell Buck that they can’t find the workers to operate and maintain manual equipment. “You just have to automate; every company has to have an automation plan,” he said.
OEM Fabricators’ plan involves using robotics to expedite basic welding tasks and maximize the talents of skilled welders earning $20 to $24 per hour. Tyler said that skilled welders are “critical to what we do”—manufacturing a variety of steel components, often in low volumes. But the speed and precision of the robotic welder OEM installed last year makes it ideal for producing large quantities of identical parts. Automating this grunt work has increased output, saved thousands of hours of labor and freed welders to focus on more complex jobs that demand human design and problem-solving skills.
Enhanced employee satisfaction has been a side benefit, Tyler said: “We haven’t seen much pushback on going to the robot because they know that the jobs that are going to the robot are the boring things.”
After about a year of service, the robot is operating at nearly full capacity; OEM plans to buy another, more expensive unit with greater capabilities later this year.
Other firms in the district delving into automation in part because of the unavailability or rising cost of labor include Distinctive Countertops in Kalispell, Mont., and Cass Precision Machining in Brooklyn Center, Minn.
Manufacturing kitchen countertops and other products made from natural stone was long a hands-on industry dependent on the skills of individual craft workers. But over the past 10 years, technology has taken much of the labor out of cutting and shaping stone.
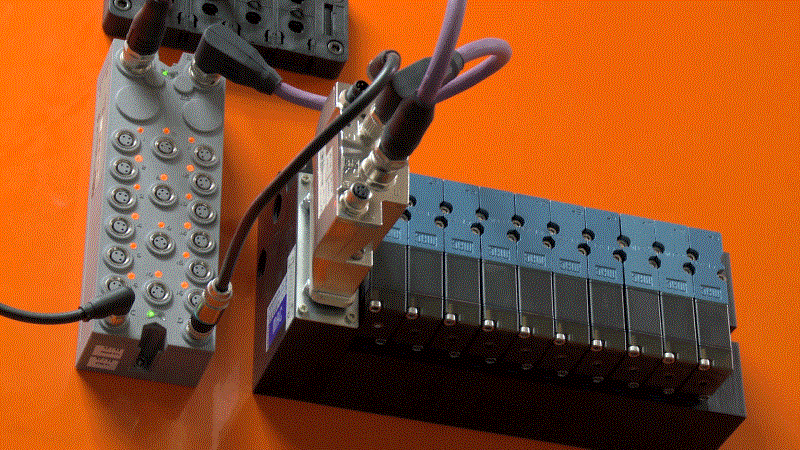
Family-owned Distinctive Countertops has invested heavily in automation since the recession, when the housing bust slashed revenues and forced the firm to lay off staff. Finding workers has always been difficult in thinly populated northwestern Montana, said President Randy Hinzman. “We don’t have the labor pool to draw from like we might in a larger metropolitan area. We knew that when [demand] started to come back, we were going to have more automation and not depend as much on skilled labor.”
Computer-controlled saws and waterjets following a digital template cut stone slabs and carve out sink and faucet holes much faster and more accurately than manual tools, greatly reducing the labor required to turn out a countertop and cutting waste to boot.
Last year, company sales were about $2.1 million—close to prerecession levels. But the firm had far fewer workers—16 compared with 26 before the recession. “You’re kind of paying for your labor upfront,” Hinzman said. “Within a couple of years, you’ve recovered those costs, and then you’re making decent money.”
Cass Precision, a manufacturer of parts for the construction and off-road vehicle industries, has upgraded its arsenal of computer-controlled mills and lathes in recent years, but this year “is going to be our big thrust toward improving automation,” said President Jim Garvin. The 130-employee firm plans to spend over $1 million on automation-within-machines technology—devices that perform multiple functions or run continuously without supervision—and two industrial robots. “Robotics is one of those things that Cass has never really utilized before,” Garvin said. “We’re kind of taking our first infant steps into that technology.”
He foresees automation handling basic “put and take” tasks, allowing the firm to better leverage the skills of hard-to-find, well-compensated machinists. And he expects assigning machines instead of people to lift and tote heavy parts and raw materials will help reduce repetitive stress injuries and workers’ compensation claims.
Beyond hands and brains
Although increasingly scarce and expensive labor is spurring manufacturers to automate, firms are also investing in robots and other smart machines because their customers demand it. By automating, manufacturers can increase production, trim prices and turn out better quality or more complex parts and products than is possible by manual means. In the Minneapolis Fed manufacturing survey, the largest share of respondents—45 percent—said that they increased their use of automation to boost productivity.
In metal machining and fabrication, automation raises productivity by maximizing output of equipment such as computer-controlled mills and lathes. Machines minded by workers who take breaks and are subject to distractions on the shop floor may achieve only 65 percent efficiency, said Dave Brockhopp, manager of the automation department at Productivity. In contrast, automated systems that feed raw material into a machine and move finished parts along to the next step in production “keep that capital equipment running consistently through the breaks, through the shift changes,” increasing efficiency to over 90 percent in many cases, he said. Production increases, and labor and overhead cost per part falls.
Such efficiency gains are crucial for manufacturers obliged to cut prices or risk losing business. Major manufacturers typically require suppliers of components to cut prices 3 percent to 5 percent annually. “Even though right now the industry is growing and there’s a lot of manufacturing demand, the big customers out there are still putting a lot of cost pressure on a company like ours,” said Garvin of Cass Precision. “Automation is one of the ways you can continue to be more competitive.”
For some types of manufacturing, quality improvements and the development of new, innovative products are only possible through automation. Human hands and brains alone simply aren’t up to the task.
ComDel Innovation of Wahpeton, N.D., produces a variety of cutting-edge products, including drones, drug auto-injectors and parts for airliner cargo bays. CEO Jim Albrecht says automation is essential to staying relevant in technically demanding, hyper cost-conscious markets such as medicine, aerospace and telecommunications. “If we didn’t have automation, and people who know how to run those systems, we would not be in business, because we couldn’t compete.”
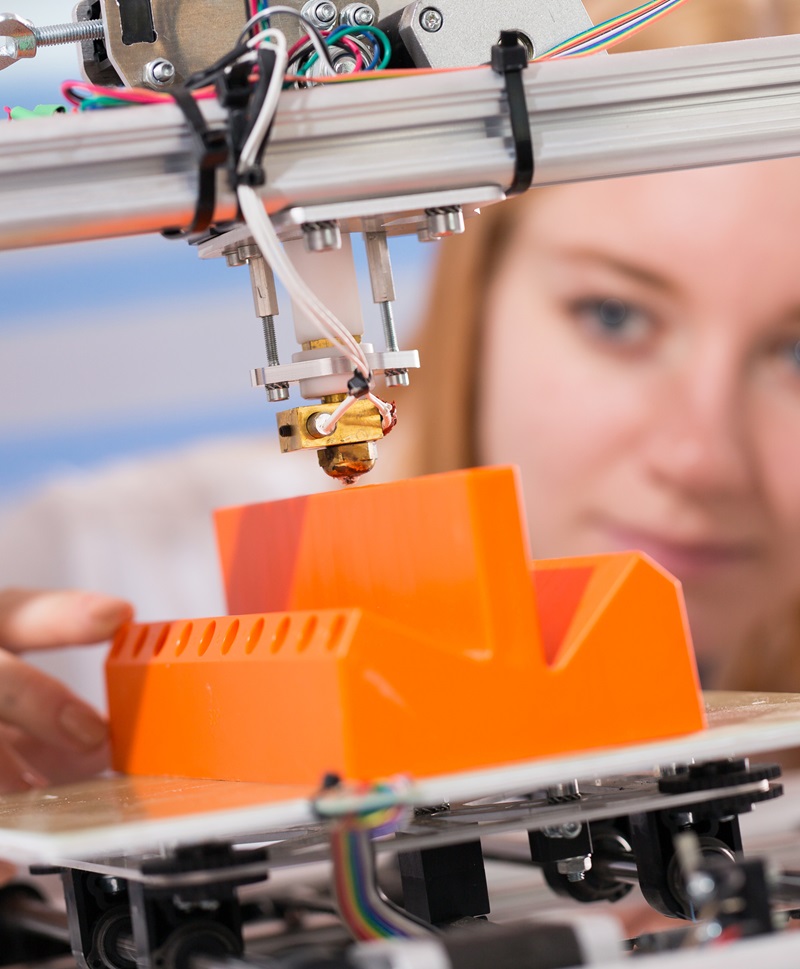
The firm spends 5 percent of its annual sales on automation and related technology, including custom automation developed in-house for specific product applications. Through automation, intricate designs can be executed with tolerances down to millionths of an inch, and large quantities produced with minimal errors. In its plastics injection molding process, ComDel uses automation to detect defective parts; a sensor inside the injection mold flags the bad part, alerting technicians to troubleshoot the equipment.
Thus, for ComDel, automation is less about labor availability and cost than meeting high expectations. “If we could find all of the people in the world,” Albrecht said, “it wouldn’t really matter because if we didn’t automate, we wouldn’t be able to achieve the quality levels that are required, produce the product at the volumes that are needed and hit the price points that our clients require.”
At Proto Labs in Maple Plain, Minn., automation is part and parcel of the business of manufacturing prototypes and parts in small quantities for medical device firms and other customers developing new products. Low-volume production has traditionally been costly, but through the use of technologies such as quick-turn injection molding and 3D printing “we can do it very cost effectively, very quickly and on demand,” said Proto Labs CEO Vicki Holt.
Compared with other forms of production, 3D printing—a process in which successive layers of material are laid down according to a digital blueprint—can turn out parts faster and in a greater variety of sizes and configurations.
Proto Labs has even automated the quoting and design process. Computer programs analyze a customer’s design and figure out how to manufacture the part, based on required materials and characteristics. “All that front-end engineering that normally takes very expensive, highly trained engineers and designers days or hours just to turn a quote, our software does it in minutes,” Holt said.
Automation anxiety—and opportunity
The factory of the future will have only two employees, a man and a dog. The man will be there to feed the dog. The dog will be there to keep the man from touching the equipment.
—Organizational consultant Warren G. Bennis
Fears that machines are destined to steal the livelihoods of humans date back to the early 1800s, when bands of textile workers in France and England destroyed labor-saving weaving machinery they blamed for unemployment and low wages. Nineteenth century British economist David Ricardo believed that workers’ anxieties about technological flux were justified; he constructed a model in which increasing investment in machinery permanently lowered demand for labor and the number of jobs.
Today, concerns are growing about the impact of automation on the workforce and income inequality. Last year, lawmakers in Hawaii voted to explore the idea of enacting a universal basic income to guarantee wages to servers, cooks and cleaners whose jobs may be replaced by machines.
Recent research suggests that automation can hurt lower-skilled workers. A 2016 study published by the Institute for Opportunity and Inclusive Growth Institute at the Minneapolis Fed found that minimum wage increases make low-wage workers doing routine cognitive tasks vulnerable to automation. Relative to other types of low-wage jobs, employment and wages fell in these occupations after the minimum wage rose, suggesting that employers substituted machines for labor.
Another study, a 2017 analysis of the impact on local labor markets of increased use of industrial robots, demonstrated an association between higher robot concentrations and reduced employment and wages.
But most research into the disruptive effects of automation focuses on short-term consequences. The history of technological innovation suggests that, over time, automation creates at least as many jobs as it destroys by lowering prices, stimulating demand and generating new employment opportunities. Each successive wave of invention—the steam engine, the light bulb, the personal computer—has given rise to new tasks performed by higher-paid workers with new job titles.
A number of district manufacturers contacted for this story had increased their head counts since stepping up their use of automation; investing in new technology and related skills contributed to higher production and revenues, resulting in more hiring.
Garvin of Cass Precision anticipates hiring more people over the next couple of years as the company’s automation initiative ramps up. “It’s not about laying people off,” he said. “It’s about growing the company and really trying to be more competitive. The more competitive you are, the better you can grow, and you’ll need to add additional workforce.”
However, automating manufacturers often hire workers with different, higher skills than the traditional machinist or welder. Increasingly, district manufacturers are looking for workers versed in robotics, motion control and other forms of automation. This year, Cass Precision plans to hire one or two automation technicians who would be responsible for programming and monitoring robotics systems. At OEM, Tyler envisions recruiting highly skilled welders (but fewer “widget welders”), automation technicians and toolmakers to build the devices that position parts for the robot welders. “Those positions we’re seeing actually increase,” he said.
Some technical colleges in the region have launched automation programs or retooled their manufacturing coursework to reflect interest in new disciplines related to automation. In 2015, Chippewa Valley Technical College, which serves an 11-county area in western Wisconsin, introduced a two-year degree in automation engineering technology. According to the college, graduates of the program earn an average annual starting salary of $53,000, and 88 percent have found a job in manufacturing or a related field within six months of graduation.
For their part, district manufacturers are reimbursing their employees for automation coursework, creating on-the-job training programs in robotics programming and other aspects of automation, and exposing high school students to career opportunities in the field.
Garvin believes that the coolness factor of automation can only help to spark interest in manufacturing among young people and overcome negative perceptions of manufacturing careers. Last October, Cass Precision hosted about 100 high school students from local schools as part of a statewide Manufacturing Day organized by a consortium of 15 higher education institutions.
“I had several students approach me during the tour, and say, ‘Who do we talk to when we graduate? We really want to come back here.’ And I asked, ‘What do you want to do?’ They pointed at a machine and said, ‘I want to run that machine right over there.’”